Reliable Samsung Washer Repair Services
Is your Samsung washer not draining, leaking, or refusing to spin? Laundry day shouldn’t be a struggle! At ZapFixers, we specialize in Samsung washer repair in Hollywood, Miami-Dade, and Broward, FL, delivering fast, reliable solutions to get your appliance running smoothly again.
Our expert technicians have experience fixing all common Samsung washer problems using genuine parts and the latest tools. Whether your washer isn’t turning on or showing error codes, we provide same-day or next-day service with transparent pricing and a warranty on all repairs.
Let ZapFixers take care of your washer — so you can get back to clean clothes without the headache!
Common Samsung Washer Issues
- Not Draining (clogged drain pump, faulty drain hose)
- Not Spinning (worn belt, motor issues, defective lid switch)
- Leaking Water (damaged door seal, loose hoses, faulty water inlet valve)
- Not Turning On (power issues, faulty control board)
- Excessive Vibration or Shaking (uneven load, worn suspension rods, leveling issues)
- Error Codes (explanation of common Samsung washer error codes like ND, UE, and 4C)
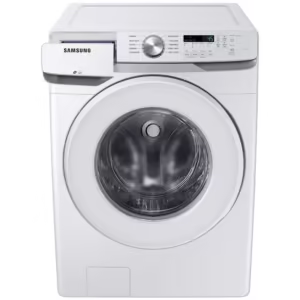
Why Choose ZapFixers for Samsung Washer Repair?
- Certified & Experienced Technicians specializing in Samsung appliances.
- Fast & Reliable Service with same-day or next-day repairs available.
- Affordable & Transparent Pricing with no hidden fees.
- OEM Parts & Warranty on repairs.
- Local & Trusted Business with great customer reviews.
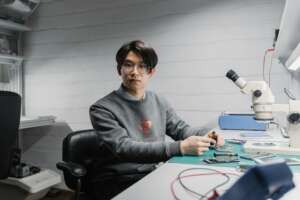
Our Repair Process
Our Samsung Washer Repair Process
At ZapFixers, we make Samsung washer repair quick, hassle-free, and reliable. Our process ensures fast turnaround times and lasting repairs:
1. Contact & Schedule
Call us or book online to schedule a same-day or next-day appointment. We work around your schedule to get your washer back in action ASAP.
2. Diagnosis & Estimate
Our technician arrives on time, inspects your Samsung washer, and pinpoints the issue. We provide a clear, upfront estimate before starting any repairs—no hidden fees!
3. Repair & Testing
We use genuine Samsung parts and professional tools to fix the issue properly the first time. After the repair, we run a full system test to ensure your washer functions perfectly.
4. Warranty & Maintenance Tips
All our repairs come with a warranty for your peace of mind. We also share expert maintenance tips to help keep your washer running smoothly and prevent future problems.
Samsung's Most Notorious Washer Defects
Spider Arm/Drum Support Failures
The spider arm failure in Samsung front-loading washers (particularly WF42H5000, WF45K6500, and WF45R6300 series) represents one of the most serious and expensive defects in modern washing machines. This aluminum component serves as the critical structural support connecting the inner stainless steel drum to the drive shaft.
The design flaw centers around the material choice and manufacturing process. Samsung uses an aluminum alloy for the spider arm that is highly susceptible to galvanic corrosion when in contact with the stainless steel drum and exposure to detergents. The resulting chemical reaction gradually weakens the metal, leading to microscopic cracks that eventually become catastrophic failures.
Owners typically first notice a subtle clicking sound during spin cycles that progressively worsens into loud banging or grinding noises as the spider arm deteriorates. By the time these symptoms become obvious, significant damage has usually occurred. Complete failure results in the drum becoming detached from the motor shaft, rendering the machine unusable and potentially causing additional internal damage.
The repair process is exceptionally invasive, requiring nearly complete disassembly of the washer. Labor costs are high due to the extensive disassembly required, and the part itself is expensive. Total repair costs typically range from $250-450, which often approaches 50% of the original purchase price of many models, making the repair economically questionable for older units.
Class action lawsuits have been filed against Samsung regarding this issue, alleging the company knew about the design defect but continued using the susceptible aluminum components. Some settlements have provided extended warranties specifically for this component, though many consumers remain unaware of their eligibility.
“Waterproof” Recall (2016)
In November 2016, Samsung issued one of the largest appliance recalls in history, affecting approximately 2.8 million top-loading washers manufactured between March 2011 and October 2016. These machines earned the sardonic nickname “waterproof” washers among repair technicians because the tops could literally become projectiles during operation.
The fundamental design flaw involved inadequate securing of the top portion of the washer to the chassis. During high-speed spin cycles, particularly when washing bulky items like comforters or heavy blankets, the machines could experience extreme vibration. This vibration could cause the top to violently detach, posing significant safety hazards to anyone nearby.
The Consumer Product Safety Commission (CPSC) received 733 reports of washing machines experiencing excessive vibration or the top detaching from the washer chassis. These incidents resulted in nine reported injuries, including a broken jaw, injured shoulder, and various impact and fall-related injuries.
The recall affected 34 different model numbers across multiple product lines. Samsung offered affected customers two remediation options: either a free in-home repair to reinforce the top of the washer, or a rebate toward the purchase of a new Samsung or other brand washing machine. The rebate came with a free installation of the new unit and removal of the old one.
The financial impact on Samsung was substantial, with recall-related costs estimated at over $450 million. More significantly, the recall damaged consumer confidence in Samsung’s appliance division, which was simultaneously dealing with the Galaxy Note 7 smartphone recall due to battery fires.
Control Board Failures
Electronic control board failures represent one of the most common issues across multiple Samsung washer models, with particularly high failure rates in the WF410ANW, WF42H5200, and WF45H6300 series. These sophisticated circuit boards control everything from cycle selection to water temperature and motor operation.
The primary cause of failure stems from inadequate moisture protection. Despite operating in inherently humid environments, many Samsung control boards lack sufficient conformal coating or proper sealing. Over time, moisture infiltration causes corrosion on circuit pathways, leading to short circuits or component failure. Additionally, the boards are often positioned near the top of the machine where steam can accumulate during hot water cycles.
Symptoms of control board failure include:
- Unresponsive or erratic control panel behavior
- Random starting and stopping of cycles
- Error codes displaying without apparent cause
- Complete power failure despite functioning electrical supply
- Cycles running incorrectly (wrong water temperature, spin speed, etc.)
Replacement control boards typically cost $150-200 for the part alone, with labor adding another $50-100. Total repair costs usually range from $200-300. Most frustratingly for consumers, these failures frequently occur just after the standard one-year warranty expires, leading to suspicions of planned obsolescence.
Samsung has made incremental improvements to control board protection in newer models, but the issue persists across many of their washing machines. Third-party repair services sometimes offer board repair rather than replacement, which can save consumers approximately 50% of replacement costs.
Door Lock Mechanism Issues
The door lock mechanism on Samsung front-loading washers, particularly evident in WF42H5000 and WF45K6500 series models, represents a critical failure point that can completely disable the machine despite being a relatively simple component.
This system combines mechanical latching with electrical sensing to ensure the door remains securely closed during operation. The mechanism includes:
- A mechanical latch hook
- An electrical switch that signals when the door is properly closed
- A locking solenoid that prevents the door from being opened during operation
- A wiring harness connecting to the control board
The design flaw primarily involves the plastic components used in the latch assembly. Repeated use causes stress and eventual fracturing of these plastic parts. Additionally, the electrical switch contacts often become corroded or misaligned, causing the washer to falsely detect an open door condition.
When this system fails, the washer typically displays a “door open” or “dL” error code and refuses to start any cycle. Many owners attempt numerous workarounds like slamming the door or applying pressure to different areas, which temporarily realigns the components but ultimately accelerates failure.
The complete door lock assembly costs between $70-90, with labor adding another $30-60, bringing total repair costs to $100-150. While not the most expensive repair, the frequency of this failure across multiple model years indicates a persistent design weakness that Samsung has been slow to address.
Some newer models have incorporated more durable metal components in the latch mechanism, but problems persist with the electrical sensing portions of the system.
Balance Ring Leaks
Samsung front-loading washers utilize a water-filled balance ring at the top of the drum to counteract vibration during high-speed spin cycles. This design feature, while effective when functioning properly, becomes a significant liability when it fails, particularly in WF45K6500 and WF45R6300 models.
The balance ring consists of a hollow plastic channel that encircles the upper portion of the drum. This channel is filled with a specific amount of water during manufacturing and then permanently sealed. The weight and movement of this water helps compensate for unbalanced loads, theoretically reducing noise and preventing the washer from “walking” during operation.
The fundamental flaw in this design involves both material quality and sealing methods. The plastic used in many models becomes brittle over time due to constant exposure to temperature fluctuations. Additionally, the seams where the ring is sealed together can develop microscopic cracks from the repeated stress of spin cycles.
When the balance ring leaks, water pools at the bottom of the washer tub. This water can:
- Damage the main control board if it’s mounted low in the machine
- Cause rust on metal components throughout the washer
- Trigger moisture sensors, leading to error codes
- Create perfect conditions for mold and mildew growth
- Eventually leak onto flooring, causing property damage
Repairing this issue requires substantial disassembly of the washer, as the entire drum unit must be removed to access the balance ring. Due to the design, the ring cannot be repaired—only replaced entirely. The part itself costs $150-200, with labor adding another $100-150, bringing the total repair cost to $250-350.
Some owners have reported multiple balance ring failures on the same machine, suggesting the replacement parts suffer from the same design deficiencies as the originals.
VRT Plus Technology Problems
Samsung’s Vibration Reduction Technology Plus (VRT Plus) represents one of the brand’s most heavily marketed features in their premium washing machines. Ironically, this system designed to reduce noise and vibration frequently becomes the source of excessive noise and movement, particularly in the WF50K7500 series.
The VRT Plus system consists of:
- Multiple stainless steel balls in a circular track that move counter to drum rotation
- An enhanced suspension system with stronger springs and shock absorbers
- Specialized sensors that detect imbalance and adjust spinning patterns
- Reinforced chassis design to minimize vibration transfer
The failure points in this complex system are numerous. The ball bearings can become dislodged from their track or break entirely. The suspension components, despite being “enhanced,” often fail prematurely due to the substantial stress of stopping and starting a water-filled drum during various cycle phases.
When the VRT Plus system fails, owners experience:
- Excessive shaking and “walking” of the machine, sometimes several feet during a cycle
- Loud banging or knocking sounds during spin cycles
- Water leakage due to stress on internal components
- Premature wear on other mechanical parts due to uncontrolled movement
- In extreme cases, damage to flooring or adjacent cabinetry
Repairing a failed VRT Plus system is labor-intensive, requiring significant disassembly to access the suspension components. Parts costs range from $150-200, with labor adding another $100-200, bringing total repair costs to $250-400.
Consumer complaints about these failures have been particularly vocal because the VRT Plus feature adds a premium of $100-200 to the purchase price of affected models. When this premium feature fails—often within 2-4 years of purchase—customers feel doubly aggrieved at paying extra for a feature that ultimately reduces the lifespan of their appliance.
Self-Clean+ Cycle Issues
The Self-Clean+ cycle featured on many Samsung washers (particularly the WF45R6300 series) promises to eliminate the common problem of mold and mildew buildup in front-loading washers. However, this heavily marketed feature frequently fails to perform as advertised, leading to persistent odor problems and potential health concerns.
The Self-Clean+ cycle is designed to:
- Heat water to near-boiling temperatures (up to 150°F/65°C)
- Agitate this hot water throughout the drum and detergent dispenser
- Create a sanitizing environment without bleach or harsh chemicals
- Run through multiple rinse cycles to remove residue
- Complete a high-speed spin to eliminate remaining moisture
The most common failure involves the temperature sensor and heating element system. These components frequently malfunction, preventing the water from reaching truly sanitizing temperatures. Without sufficient heat, the cycle essentially becomes an extended rinse that fails to kill bacteria or remove biofilm buildup.
Owners typically discover the issue when:
- Persistent mold spots appear on door gaskets despite regular Self-Clean+ cycles
- Laundry emerges with a musty odor despite washing with detergent
- Visible slime or biofilm develops in crevices around the drum
- The washer itself emits unpleasant odors, especially when closed
The temperature sensor costs approximately $40-60, while the heating element runs $80-120. With labor, repairs typically cost $150-250. However, many owners simply abandon using the feature rather than pursuing repairs, instead adopting manual cleaning routines with vinegar or commercial washing machine cleaners.
Samsung has faced multiple class-action lawsuits regarding misleading advertising of the Self-Clean+ function, with some cases resulting in settlements offering partial refunds or extended warranties specifically covering the heating components.
“Suds Lock” Detection Failures
Samsung’s high-efficiency washers incorporate a “suds lock” detection system designed to prevent damage from excessive soap buildup. However, this system is notorious for hypersensitivity, particularly in the WF45K6500 series, causing frustrating interruptions to normal washing cycles.
The suds detection system utilizes:
- Pressure sensors to monitor water levels
- Flow meters to track water movement
- Programming that analyzes drum resistance during agitation
- Multiple rinse protocols when excess suds are detected
The system frequently triggers false positives due to several factors:
- Malfunctioning pressure sensors that misinterpret normal water conditions
- Algorithmic flaws that misidentify normal water turbulence as suds
- Excessive sensitivity to mineral content in hard water areas
- Inconsistent calibration between production batches
When a false suds lock is detected, the machine enters an extended rinse cycle that can add 30-45 minutes to washing time. In more severe cases, the machine displays an error code (typically “Sud” or “Sd”) and stops entirely, requiring manual intervention to restart.
This issue is particularly frustrating because it creates a no-win situation for consumers. Using the manufacturer-recommended amount of HE detergent often results in inadequate cleaning, while adding more detergent triggers the suds lock. Additionally, the extended rinse cycles significantly increase water consumption, undermining the efficiency claims of these “high-efficiency” machines.
The pressure sensor component costs $50-70, while reprogramming the control board (when possible) costs $80-120. Total repair costs typically range from $130-200. However, many consumers resort to workarounds like using minimal detergent and adding it directly to the drum rather than the dispenser.
Samsung has quietly modified the suds detection algorithms in newer models, but has never acknowledged the hypersensitivity issues in affected models or offered a formal fix through firmware updates.
Preventative Maintenance Tips for Samsung Washers
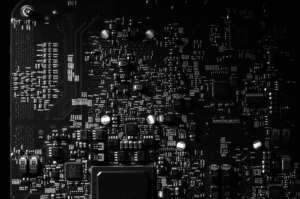
- Clean the washer drum and door gasket regularly.
- Use HE detergent to prevent excess suds.
- Inspect and clean the drain pump filter.
- Check and tighten hoses periodically to prevent leaks.
- Avoid overloading to prevent excessive wear.